18XT Front Differential
I designed, optimized, and manufactured a fully custom front differential for JHU's Baja SAE team.
Project Overview
I began my design process by performing a detailed trade study evaluating different types of differentials used in commercial off-roaders as well as by previous Hopkins Baja vehicles. Based on, our performance and competitive goals, I used a quantitative decision matrix process based on weighted values for each of our performance metrics.
I ultimately decided on a system architecture based on overrunning clutches on each front half shaft. It features a pair of custom spiral bevel gears coupled to an aluminum cage into which sprag clutches are inserted and used to drive each output shaft. The sprag clutches allow the outside wheel to overrun the inside wheel on turns while also allowing the whole differential to lock up instantaneously, whenever the rear wheels lose traction.
This system provides the traction performance of a front spool and the maneuverability of an open differential, all in a lightweight package with few points of failure.

Differential Design

Custom Bevel Gear Design
I used the following spreadsheet to do hand calculations to design the tooth geometry for the bevel gears in the front diff, optimizing for the lifetime that they would see over three competitions of use. I followed AGMA standards for bevel gears to calculate the contact and bending stress the teeth would see. I then validated these calculations in KISSsoft.
Case Analysis
I used ANSYS to set up an assembly-level FEA to analyze the front diff cases for stress and deflection. The max load from the bevel gears was applied to the bearing surfaces while the frame tab mounting points were fixed. I optimized wall thicknesses and added ribbing until the case was within its component allowable stress and deflection.

Stress plot of differential cases with maximum locations called out
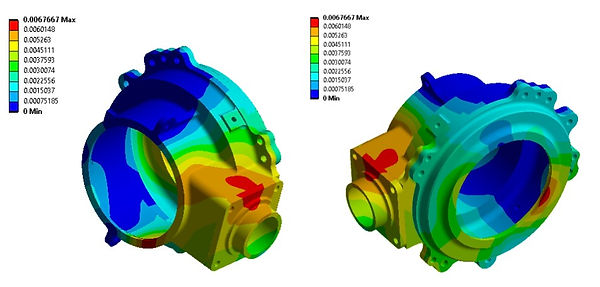
Deflection plot of differential cases

Manufacturing

I manufactured the diff cage primarily with a manual lathe, with the internal keyway being cut on a wire EDM as a secondary operation. The ring gear blanks and case were machined on a 3-axis CNC mill, and the pinion blank on a CNC lathe. I found a sponsor to face mill the bevel gear teeth into each gear blank and then case-harden them before lapping each gear pair into a perfectly matched set. After receiving the completed gears, I assembled the case and tested it's functionality before installing it in the car and testing it under load.
Final differential case, gears, and cage


Turning the cage
CNC machined case sections
Competition and Results
I presented the design of my custom front differential at all three 2022 Baja SAE competitions, where the team earned one 1st place finish and two 2nd place finishes in the design category. The 4WD capabilities of the vehicle were showcased throughout the suspension & traction and endurance events, where the 18XT was able to pull itself out of tough spots where a 2WD vehicle would have gotten stuck.
​
The 18XT recently competed in the Fall 2022 Arizona competition, earning 8th place overall!
